Offshore Aquaculture
Verifying New Fish Farm Designs with Fiber-Optics
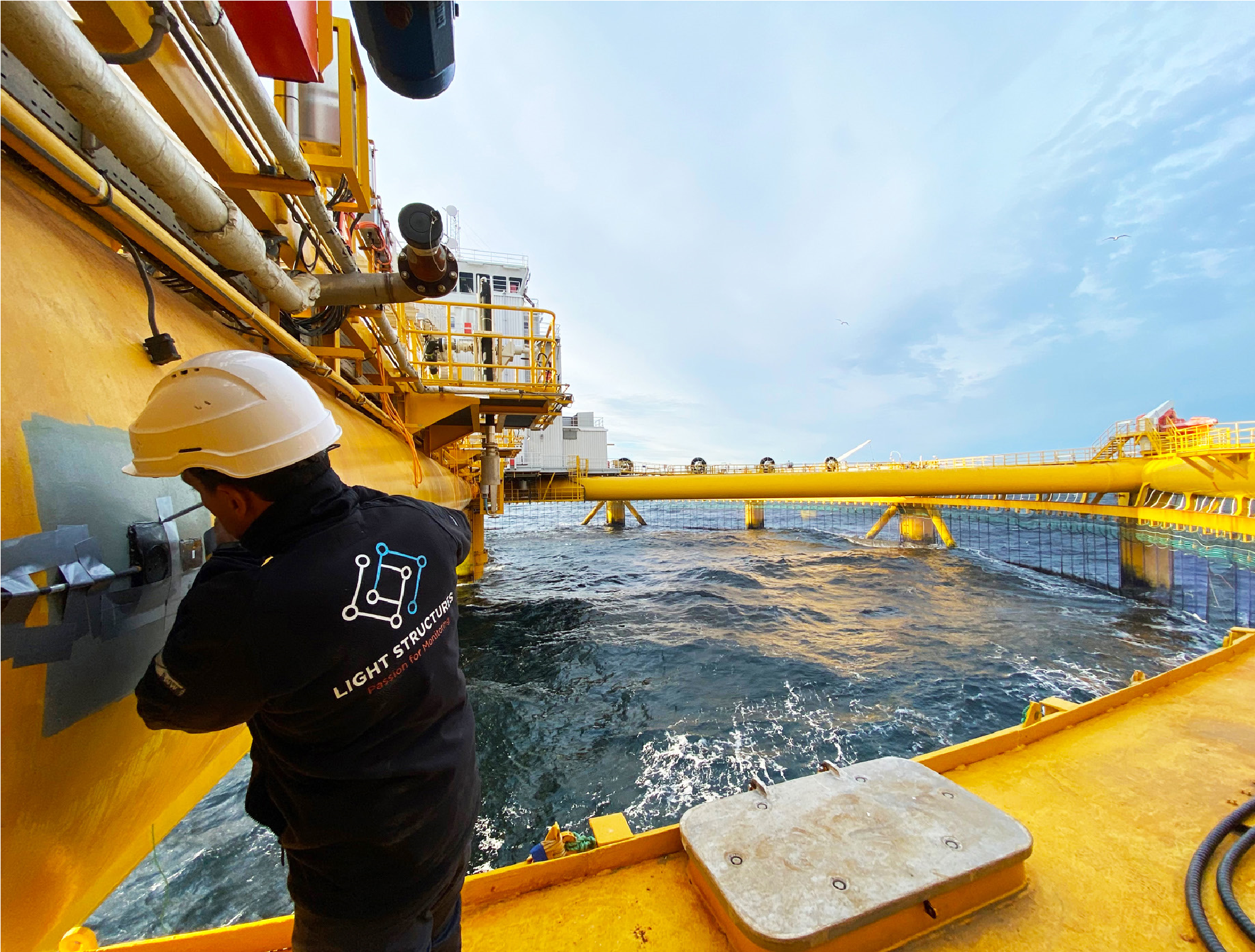
Verifying New Fish Farm Designs with Fiber-Optics
By Ernad Sehic
Lack of space for more freshwater and coastal marine sites, new legislation and growing demand for more fish and seafood production globally are driving the creation of innovative fish farm designs for deeper offshore waters. The transition to so-called “exposed aquaculture” is not without difficulty, with the frequency and severity of structural fatigue caused by the impact of inclement weather and high seas firmly at the top of the design criteria for proposed new fish farms, including the world’s first such offshore facility, Ocean Farm 1. Making its debut as the first-ever offshore fish farm
in 2017, at 68 m high with a diameter of 110 m and
250,000 m3 volume, Ocean Farm 1 is a full-scale pilot facility designed to verify the biological and technological aspects of offshore fish farming. Located in open water near Frohavet on Norway’s west coast, it has already demonstrated that the “exposed fish farm” concept introduces tangible benefits to the aquaculture workflow, not least with the ability to raise healthier fish due to the continuous flow of water an offshore location enables.
Offshore Pilot Facility
Having partnered with Ocean Farming AS, the operat-
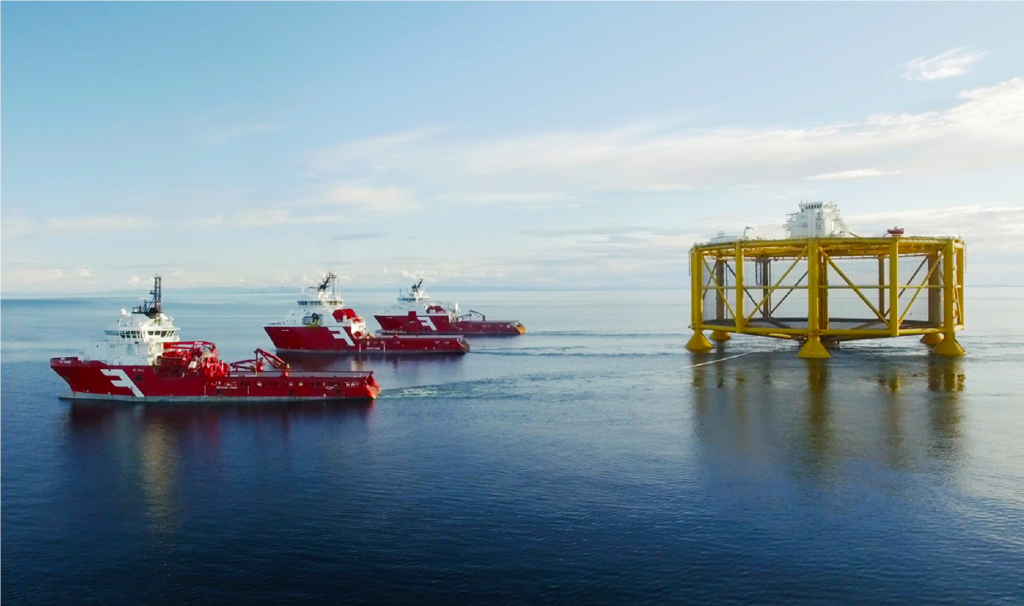
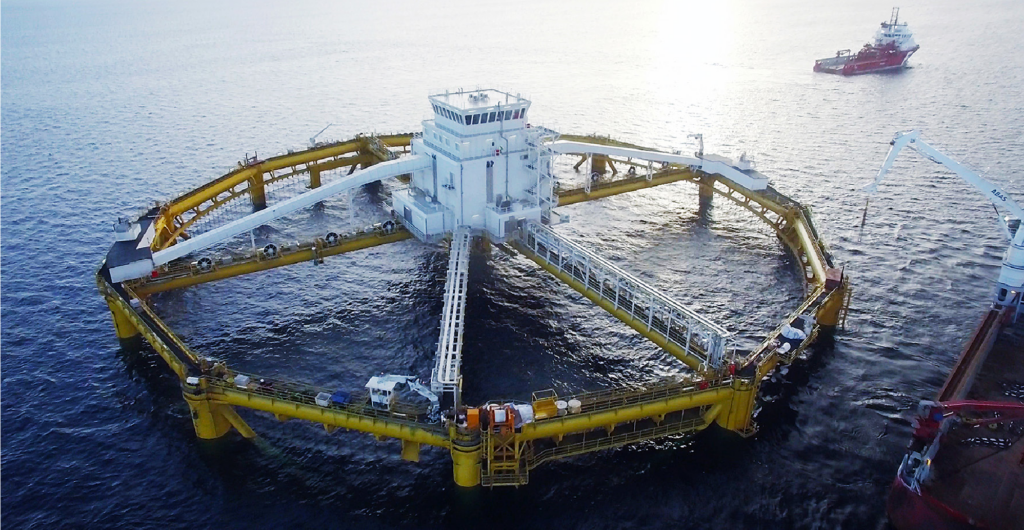
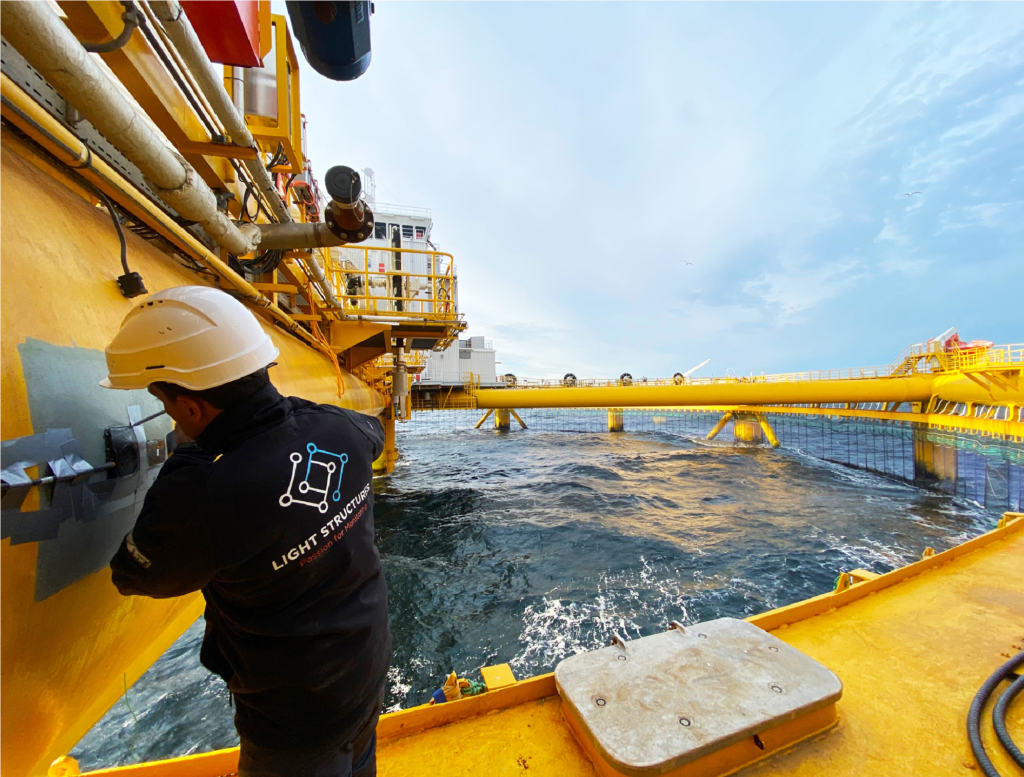
have been installed on site. (Credit: SalMar)
ing company established by Norway-based SalMar ASA, since the very beginning of the Ocean Farm 1 development project, Norwegian maritime lassification society DNV has played an integral role within key technology, engineering and regulatory workflows. The DNV team leveraged expertise in developing systems, solutions and regulatory frameworks for offshore energy production, but a huge amount of application
-specific innovations and processes were needed to ensure safety and efficiency in the building and operation of Ocean Farm 1. With the main goal of any fish farm to have a large, safe volume of water where fish can be produced, new structures designed for offshore aquaculture are far removed from their counterparts in the offshore energy sector. As the first structure of its kind, Ocean Farm 1
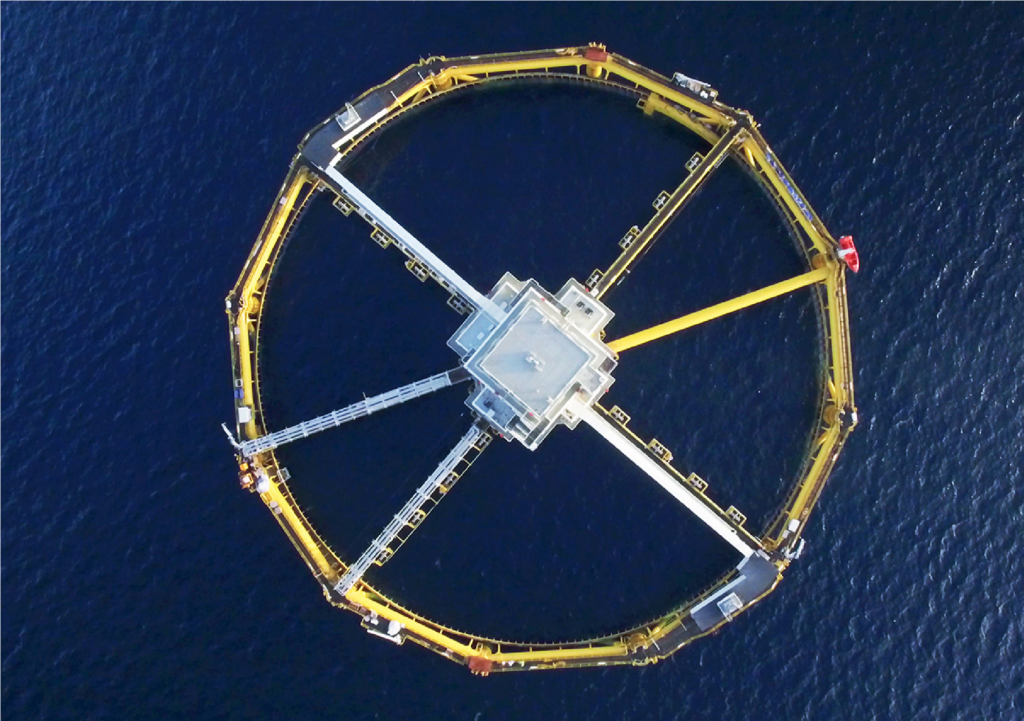
development was undertaken using limited information and experience on the impact of the increased motion and load caused by the offshore environment. Thus, SalMar esignated Ocean Farm 1 as a pilot facility. Its operation to date has returned significant data that have contributed to a greater understanding of how to deal with structural loads that a standard fish farm would never encounter. The data lead to Ocean Farm 1 updates and the development of new exposed fish farm concepts. But there is still a lot more to learn. In order to provide more precise structural stress and fatigue data for lifecycle research conducted by DNV, SalMar tasked structural measurement specialist Light Structures to deliver a customized monitoring system using its SENSFIB technology in August 2021.
The new system is based on fiber-optic technology that applies the fiber Bragg grating (FBG) methodology to introduce more granularity than traditional lectromechanical systems. Sixteen high-precision fiber-optic sensors from Light Structures’ SENSFIB technology range have since been installed on Ocean Farm 1.
The decision to use this unique alternative to traditional electromechanical structural monitoring was made based on the better accuracy, dependability and adaptability of FBG, as well as DNV’s previous experience of hull stress and fatigue monitoring with Light Structures. Through the use of SENSFIB technology, DNV is now working to improve knowledge of fatigue-sensitive areas and how this contributes to making inspection
plans that reduce the risk of fatigue damage and the cost of inspections.
Fatigue and Overloading
Having already contributed significantly to, e.g., concept evaluations, defining the regulatory framework, verification and certification of the structure and mooring
system, and class uptake, DNV is well placed to extractvalue from the SENSFIB data in a study that is vital not just for the future of Ocean Farm 1 but for the future of offshore fish farming.
DNV’s workflows and processes, which are enabledin part by the improvement in structural load data, include a risk-based inspection plan for the steel structure and upgrades to the measured response.
When measuring integrity and reliability, SENSFIB data can help to reveal the conditions of a structure and potential damage sources, fatigue cracking and overloading that could cause yielding, buckling and rupture. The data can also help with supporting aspects, including, for example, operating within safe limits and safe weather windows.
These insights are related to maintenance and safety, but the same data may also be useful to provide input to surveys for inspection planning of scope, extent and focus. For example, a single extreme event may reveal the need for an immediate inspection, while generally low and favorable conditions may justify extended survey intervals.
“Ocean Farm 1 is just the start of a new era of exposed aquaculture:
Its inception, development and operation will provide
a knowledge platform that will have an impact far and wide.”
Securing Dependable Stress Data
Considering that traditional electromechanical measurement systems are more prone to failure in the maritime environment, Light Structures uses FBG to offer a more dependable data stream for its clients. SENSFIB is deployed on more than 300 vessels/platforms globally.
FBG sensors are small and intrinsically safe, so they can be installed practically anywhere, including vessels and hazardous zones covered by ATEX (explosive environment) regulation. They are also immune to electromagnetic interference for reliability, and because FBG systems measure the wavelength of light, they provide the most accurate stress measurements possible.
While each installation is an in-depth custom project led by Light Structures’ experts based on the specific monitoring requirements of the customer, SENSFIB’s fiber-optic stress monitoring sensors are practically fit and forget. They need no recalibration, and the maintenance burden is much lower than alternative systems because there are no moving parts. Importantly, no welding is needed for installation, which further lowers ownership costs and enables easier expansion to include, e.g., fatigue monitoring in the water line and bow sensors for ice load monitoring.
Integrated Data Challenges
While classification society interest in structural stressmonitoring continues, there are currently no regulations demanding its use on special platforms such as Ocean Farm 1 or on ships of any size or specific structural loading risk. However, there are already rules for inspections based on condition monitoring of structures for offshore units and floating wind turbines, which may be applied to fish farms. They take a quantitative risk-based approach combining sensor data with design models to help define inspection intervals for critical details subject to nondestructive testing. This is mainly related to fatigue cracking but potentially also overloading. Corrosion and other damage modes need to be covered by other approaches.
Reflecting the potential to combine and integrate disparate data sets, DNV’s Veracity cloud platform has become an important aspect of Ocean Farm 1’s structural monitoring in recent months. SENSFIB data are sent to Veracity once per day, where they are stored safely and can easily be shared with DNV, SalMar engineers or third-party consultants, including Light Structures’ experts. Veracity also provides a platform for improving insight based on data trends, and it is possible to add new data streams from other sensors or communications channels (weather, motion, currents, etc.) should they be required going forward.
To deliver added value, there must be complete trust in all data coming through the system; for instance, the data must not be tampered with, and the quality should be according to expectations. These concerns are an issue for all sensor-based systems and also apply to structural load monitoring. The system itself and the data from each sensor network need to be verified against requirements addressing quality and security for class systematics and important decisions; cyber secure is a class notation for this, and D-INF is a class notation for the data collection infrastructure. SENSFIB may then be a part of a larger system, with sensor data coming from many systems
Increasing Production Capacity
Ocean Farm 1 is just the start of a new era of exposed aquaculture: Its inception, development and operation will provide a knowledge platform that will have an impact far and wide. The United Nations predicts that the world will need 70 percent more food by 2030, at the same time as tackling lowering global emissions and aiming to achieve the UN’s Sustainable Development Goals.
SalMar Aker Ocean, the new company formed by SalMar AS and offshore engineering and operations specialist Aker for the operation of Ocean Farm 1 and subsequent new offshore aquaculture concepts, aims to establish sustainable production of approximately 150,000 tonnes of salmon in offshore and semioffshore sites by the end of 2030, securing Norway’s position as a key fish and seafood producer.
SalMar is confident that precise structural stress and fatigue measurement by Light Structures will provide a significant contribution to the development of structural modifications and alternative offshore fish farm designs, as well as new processes and workflows that will strengthen the case for taking aquaculture further from shore.
DNV will ensure that SalMar Aker Ocean can leverage the SENSFIB data into actionable insight and decision support through ongoing development of structural monitoring with SENSFIB technology. And the in-depth experience of Light Structures’ technology on Ocean Farm 1 is helping to prepare SENSFIB for safety and risk reduction in the day-to-day operations of advanced new fish farms that we are yet to imagine. ST
Ernad Sehic is senior international sales manager at Light Structures AS. He is based at the maritime structural stress monitoring company’s Oslo headquarters. Sehic joined in 2017 as a project manager after spending 10 years in various hands-on project management and engineering roles at National Oilwell Varco.
© 2022 Compass Publications Inc. Sea Technology (ISSN 0093-3651) is published monthly by Compass Publications Inc., 4600 N. Fairfax Dr., Suite 304, Arlington, VA 22203; (703) 524-3136; oceanbiz@sea-technology.com. All rights reserved. Neither this publication nor any part of it may be reproduced, stored in a retrieval system, or transmitted in any form or by any means, electronic, mechanical, photocopying, recording, or otherwise, without the prior permission of Compass Publications Inc.