Custom Projects: Structural Monitoring for Diverse Maritime Assets
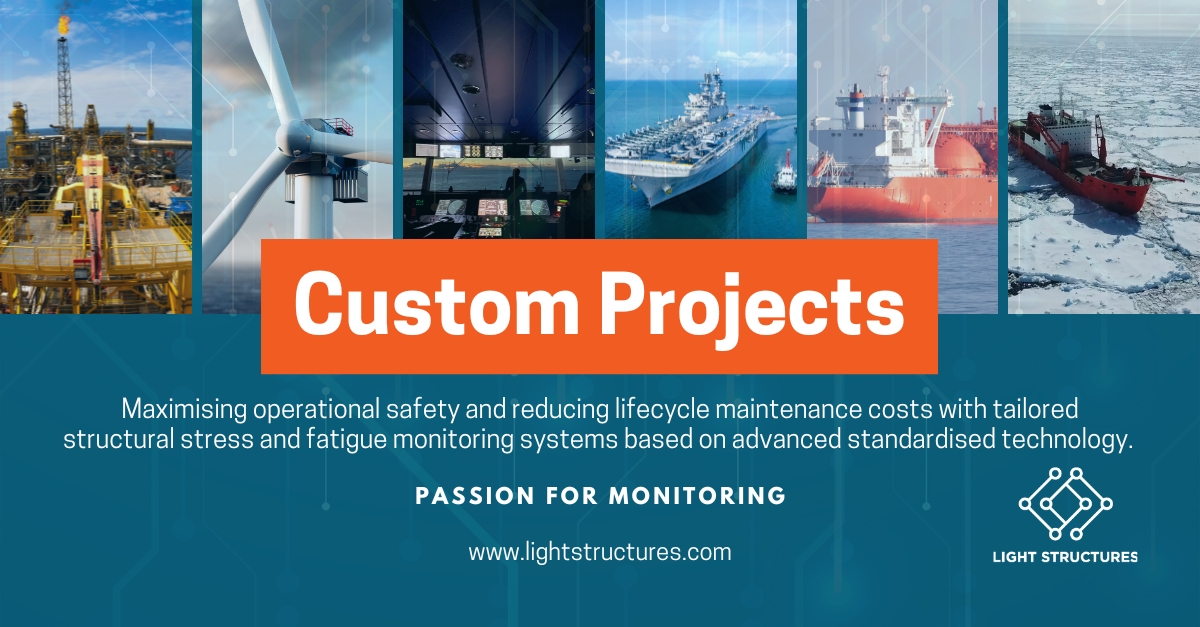
The maritime environment is harsh on man made structures like ships and wind turbines. The constant exposure to saltwater, fluctuating temperatures, and relentless mechanical stress significantly contributes to structural damage, fatigue and corrosion. This damage often begins as microscopic cracks or localized corrosion, which can propagate over time, compromising the vessel’s or structure’s overall integrity.
If left unchecked, these small issues can escalate into catastrophic failures, leading to severe environmental damage, costly repairs, and the potential loss of human life. Effective monitoring and maintenance are thus essential to mitigate these risks and ensure long-term operational safety.
A sensor and technology foundation
Monitoring structural stress and fatigue is a complex task that requires precise, real-time data to be most effective. The SENSFIB system offers a robust solution for the challenge. Utilizing advanced fiber optic sensors, SENSFIB provides continuous, real-time measurements of stress and fatigue across a vessel’s structure. Unlike traditional methods that rely on periodic inspections, SENSFIB delivers accurate data 24/7, allowing for immediate detection of anomalies and proactive maintenance.
The system’s sensors are highly sensitive and reliable, immune to electromagnetic interference, and require minimal recalibration, ensuring consistent performance in various conditions. By integrating this data into digital systems and predictive maintenance algorithms, operators can anticipate potential failures and schedule maintenance before critical issues arise, thus optimizing operational efficiency and safety.
Adaptable solutions for diverse structures
One of the standout features of the SENSFIB system is its adaptability to different maritime assets, making it an ideal choice for a wide range of vessels and offshore structures. For instance, FPSOs (Floating Production Storage and Offloading units) benefit from SENSFIB’s ability to monitor low-cycle fatigue caused by loading and offloading sequences. Ice-class vessels, operating in polar regions, face unique challenges from ice-induced stresses; SENSFIB’s real-time monitoring ensures these vessels can withstand such harsh conditions.
LNG tankers, prone to the effects of LNG sloshing, can rely on SENSFIB to detect and mitigate the structural impacts of these dynamic loads. Additionally, offshore wind turbines, which endure constant wind and wave forces, can use SENSFIB to monitor integrity at the foundation and surface level, preventing unexpected failures and ensuring continuous energy production.
Delivering countless custom projects
Considering the diverse applications of the SENSFIB system, it becomes clear that this technology is not just a one-size-fits-all solution but a customizable foundation adaptable to the unique requirements of each maritime asset. And in reality, every SENSFIB installation is a custom project based on a foundation of field proven, high-performance technology.
This versatility positions SENSFIB as a crucial component in the maintenance and safety protocols of most maritime vessels and structures. In our upcoming “Custom Projects” blog series, we will delve deeper into specific case studies and examples, showcasing how SENSFIB enhances the safety and efficiency of FPSOs, ice-class vessels, LNG tankers, offshore wind turbines, and more. Stay tuned for these insightful explorations, coming soon.